PRODUCTS
RHJR850 Laser processing equipment
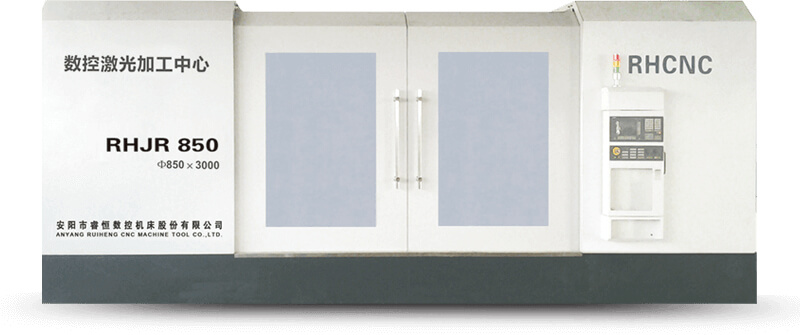
-
Swing over bed:Φ850mm
-
Maximun workpiece length:3200mm
-
Maximun turning length:3100mm
-
Span of guideway:435mm
-
Spindle bore:Φ94mm
-
Machine overall demensions:6500×2000×2640mm

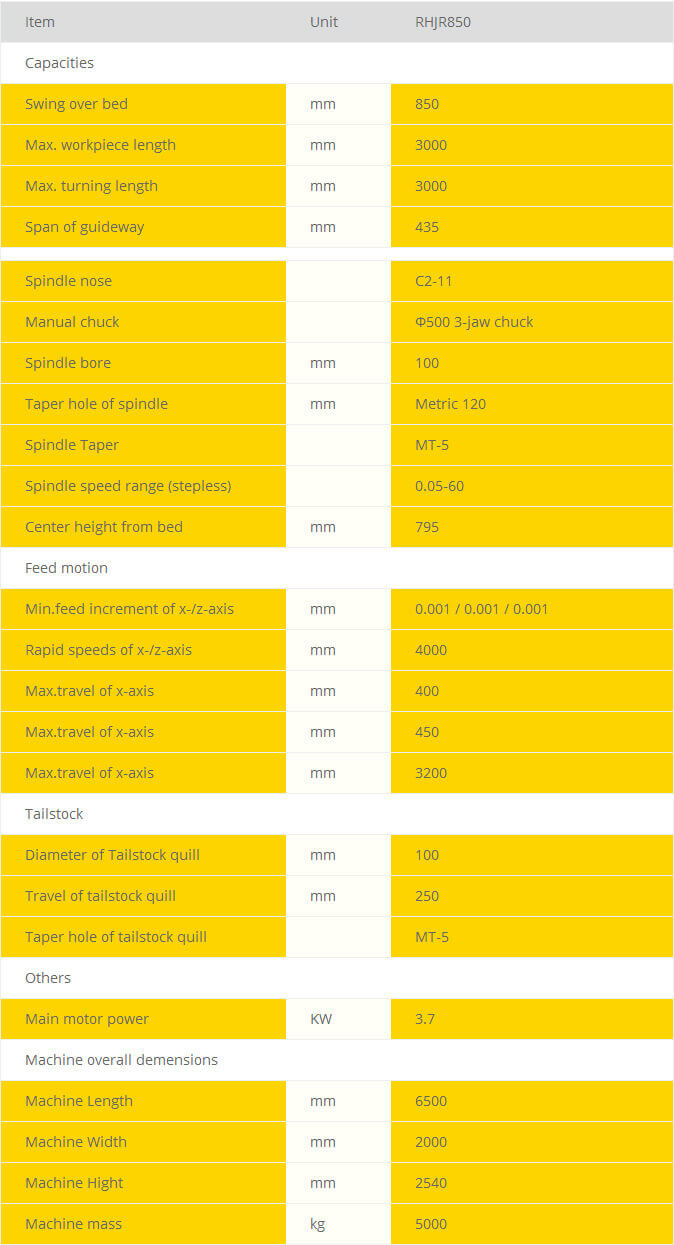
Laser Cladding is a weld build-up process and a complementing coating technology to thermal spray. It is increasingly used instead of PTA (Plasma Transferred Arc) welding and easily outperforms conventional welding methods like TIG (Tungsten Inert Gas) for advanced weld repair applications. Due to its superior focusing ability, lasers allow power densities that are not typically possible with conventional thermal procedures. This enables to process components with minimal thermal loading and distortion. Laser cladding is particularly suitable for applications demanding a high dimensional accuracy. Additional applications include materials that are difficult to weld using conventional methods, such as high temperature-resistant nickel-based alloys in gas turbines or tungsten-carbide-filled wear-protection coatings. Typical components include turbine blades, drilling equipment, and pump components. Ruiheng Laser Cladding Process In laser cladding, the laser beam is defocused on the workpiece with a selected spot size. The powder coating material is carried by an inert gas through a powder nozzle into the melt pool. The laser optics and powder nozzle are moved across the workpiece surface to deposit single tracks, complete layers or even high-volume build-ups.
Key Characteristics
- Perfect metallurgically bonded and fully dense coatings
- Minimal heat affected zone and low dilution between the substrate and filler material resulting in functional coatings that perform at reduced thickness, so fewer layers are applied
- Fine, homogeneous microstructure resulting from the rapid solidification rate that promotes wear resistance of carbide coatings
- Edge geometries can be coated and built up with welded deposits
- Near net-shape weld build-up requires little finishing effort
- Extended weldability of sensitive matierals like carbon-rich steels or nickel-based superalloys that are difficult or even impossible to weld using conventional welding processes
- Post-weld heat treatment is often eliminated as the small heat affected zone minimizes component stress
- Excellent process stability and reproducibility because it is numerical controlled welding process